When you think back to your last hospital renovation project, is is easy to separate the final accomplishment from the stressors and complications that went before it? For many construction managers and contractors, each new project brings with it so many different stakeholders and with them differing opinions, shifting timelines, endless redesigns and poor communication that it can seem like the end -- a completed, successful project -- cannot come soon enough and may indeed never come at all.
The Lean Construction methodology, with its basis in manufacturing approaches, aims to change that.
According to Healthcare Design Magazine, the Lean Construction methodology is all about “building a facility more efficiently and cost effectively without reducing scope and quality.” It would be hard to argue with the benefits of a process that could do all that. But how exactly does it work?
How Lean Construction Works
While the entire Lean Construction methodology cannot be fully explored in a single blog post, we can discuss in brief how the system works. For a more thorough accounting of the Lean Construction principles, be sure to visit the International Group for Lean Construction (IGLC) who first coined the term in 1993.
Lean Construction Starts Early
An Integrated Project Delivery (IPD) is the focal point of the lean construction process from the outset. An initial team of the project owner, architect, construction manager, design consultants, and subcontractors form an IPD group at the very beginning points of the project timeline and contribute to the project from even before the design is begun. This collaboration is essential to the process, allowing designers to work from an already established project plan that has input from all sides and thereby minimizing - or ideally eliminating - any need for redesign.
You Can’t Go it Alone
Whether you are a Construction Manager or a hospital administrator, you cannot approach Lean Construction unilaterally. Indeed, the whole point of the process is collaboration and joint efforts towards a common goal. That means that without buy-in from an entire project team, it will be impossible to fully implement the methodology and end up with a project that is more efficient.
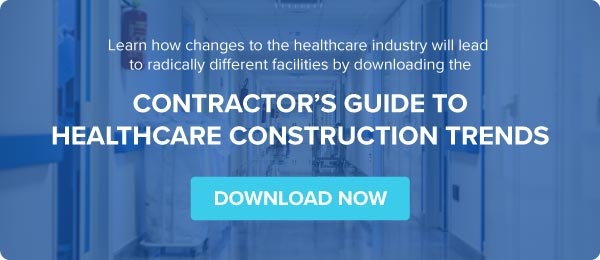
How You Can Apply Lean Construction Principles
The fact is that you may not be able to singlehandedly shift a new project from traditional hospital construction methodologies to Lean principles. But there are still ways you can apply some elements of the methodology in order to improve your next hospital renovation or construction project.
Value Team Input
One of the key ways in which lean construction differs from common construction processes is in how the IPD team coalesces around its common goal from the very beginning. If you want to bring this kind of shared vision to bear within your own construction team, it is important to demonstrate leadership while at the same time valuing the expert opinions of those that you work with -- and to do this from the very beginning. This way, concerns are addressed early on and you can mitigate the risk of costly redesigns or restructuring.
Shared Risk, Shared Reward
Lean construction methodologies call for pooled resources when it comes to potential overages or savings, meaning that it is in the best interest of all stakeholders to be as efficient as possible. While that may not be feasible in your construction process, it is important to reward those team members that make positive contributions to maintaining a schedule and budget for your project, whether that is done through financial bonuses or future opportunities.
It may be a long time before all healthcare construction projects employ a Lean Construction methodology if that happens at all. Still, the principles can give you and your team a new perspective on how to assess future projects and create a more efficient system for your own methodologies.